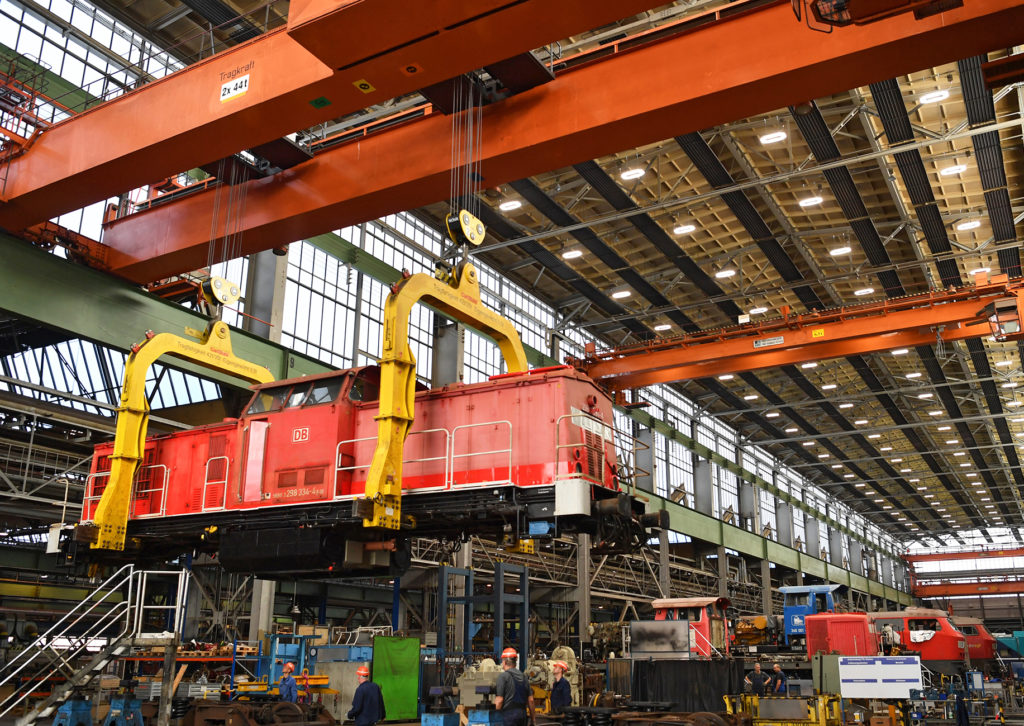
Seit 150 Jahren schreiben wir in Cottbus Eisenbahngeschichte: Das bestehende Werk in der Lausitz-Metropole wurde 1874 als „Königliche Hauptwerkstatt Kottbus“ gegründet. Die Werkstätte widmete sich der „Ausbesserung von Dampflokomotiven und Wagen“ und verfügte schnell über einen exzellenten Ruf. Diese Tradition führen wir nun fort und entwickeln das Werk radikal weiter.
Rund um den historischen Lokschuppen in Cottbus bauen wir in den nächsten Jahren das größte, modernste und umweltfreundlichste Instandhaltungswerk der DB – nicht nur in Deutschland, sondern in ganz Europa. Sichtbarstes Zeichen dafür ist die mehr als 400 Meter lange Halle, in die ein ganzer ICE-4-Zug hineinpassen wird. Die Energie für das Werk kommt zum Teil aus Photovoltaikanlagen. Der Fokus liegt auf der „schweren Instandhaltung“ – das beinhaltet insbesondere große Umbauten, Reparaturen von Unfallfahrzeugen und die großen Hauptuntersuchungen.
Vor allem aber gibt uns Cottbus die einmalige Chance, ein Werk zu bauen, das das komplette Potenzial der vierten industriellen Revolution nutzt: Ein Instandhaltungswerk, in dem innovative Sensorik, echtzeitfähige Kommunikation mit 5G, intelligente Analyse durch Künstliche Intelligenz (KI) und neue Automatisierung durch Robots und „Cobots“ von vornherein in das Werksdesign integriert sind. Die gesamten Abläufe und Prozesse werden bis hin zum Einkauf digital geplant und gesteuert. Das IH-Werk Cottbus wird ein Leuchtturm für deutsche Ingenieurskunst.
Schneller: Radikal weniger Zeit für die Reparatur
Mit dem Design dieses Werks können wir die Zeit, in der die Züge repariert werden, radikal verkürzen. Im Wesentlichen beruht dieser Effekt darauf, dass wir „vorher wissen“. Heute kommen die Züge in die Instandhaltung und erst dann wird das Ausmaß des Schadens klar. Das Phänomen hat einen Namen – der sogenannte „Ups-Effekt“ – wenn man zum Beispiel die Deckenklappen des Fahrzeugs entfernt und die darunterliegenden angescheuerten Kabel sichtbar werden. In Zukunft wissen wir vorher, welche Schäden der Zug hat und können so gezielt Teams bereitstellen und Ersatzteilbeschaffung und notfalls 3D-Drucker rechtzeitig anwerfen, um die Standzeiten so kurz wie möglich zu halten.
Mit anderen Worten: Wir erhöhen die Verfügbarkeit der Fahrzeuge für unsere Kunden. Die Züge können länger auf der Schiene unterwegs sein und stehen kürzer in der Werkstatt. Und das ist auch dringend nötig: In den nächsten Jahren wächst unsere ICE-Flotte deutlich – auf mehr als 420 Fahrzeuge bis 2026. Dafür brauchen wir neue Kapazitäten in der Instandhaltung.
Wir sind nicht allein
Wir sind auf diesem Weg nicht allein unterwegs. Die frühe Ausstattung mit einer Vielzahl von Sensoren hat dazu geführt, dass die Luftfahrtbranche bereits seit einiger Zeit automatische Datenanalysen bis hin zu Verfahren der KI bei der Wartung von Flugzeugen einsetzt. Echtzeit-Analyse von Triebwerks- und anderen Daten und maschinelles Lernen machen hier längst eine vorausschauende Wartung möglich. Die Algorithmen agieren meist als „digitale Assistenten“: Sie analysieren etwa den Zustand der Turbinen und empfehlen den Ingenieuren geeignete Schritte. Das Ziel dahinter ist klar: Flugzeuge verdienen nur Geld, wenn sie fliegen! Es gilt, den Wartungsaufwand zu verringern, die Verfügbarkeit der Flugzeuge zu erhöhen und die Flottenplanung zuverlässiger zu machen. Und das gilt für unsere Bahn-Flotten genauso.
Die smarte Instandhaltung, die wir nun in Cottbus planen, führt dazu, dass mehr Menschen mit der Bahn fahren können. Wir machen Zugreisen pünktlicher und attraktiver. Auch in einem digitalisierten und automatisierten Werk gibt es natürlich weiterhin „Schraubenschlüssel“. Aber die Arbeitsprozesse, die Planung der Kapazitäten, die Bestellung und die Lieferung von Material – das alles steuern wir digital.
Starke Schiene, starke Lausitz
Deutschland will bis 2038 aus der Kohleverstromung aussteigen. Die Deutsche Bahn unterstützt den Strukturwandel im Braunkohlenrevier Lausitz, das sich vom Süden Brandenburgs bis nach Nordsachsen erstreckt, mit einem Modernisierungsprogramm. Finanziert wird das Vorhaben auf der Basis des Strukturstärkungsgesetzes, das die Bundesregierung zusammen mit dem Kohleausstieg verabschiedet hat, um die wirtschaftlichen Folgen für die betroffenen Regionen abzumildern. Am Standort Cottbus entstehen eine neue ICE-Halle für die schwere Instandhaltung von Elektrotriebzügen (ICE4), ein Bereich für die Umrüstung von Dieselfahrzeugen auf Hybridtechnik mit Elektroantrieb sowie ein Technologiezentrum zur Hybridforschung und moderne Lehrwerkstätten. Bis 2026 sollen dort 1.200 Arbeitsplätze geschaffen werden, darunter 100 Ausbildungsplätze. Außerdem werden Bahnverbindungen von Cottbus in die umliegenden Großstädte sowie in das benachbarte Polen ausgebaut und modernisiert. Vertreter von Deutscher Bahn, der Bundesregierung und der Länder Brandenburg und Sachsen stellten die Pläne im September der Öffentlichkeit vor. |
Kameras und Sensoren erkennen Schäden
Auch die DB setzt bereits auf „predictive maintenance“ (vorausschauende Wartung) in allem Bereichen. In der Infrastruktur, also „am Gleis“, ist erst kürzlich die letzte von 28.000 smarten Weichen ans Netz gegangen, bei der wir auch die Funktionsfähigkeit der Weichenheizungen quasi per Fernbedienung – remote – kontrollieren können. Mehr und mehr Sensorik, insbesondere in den modernen Flotten wie dem ICE 4, helfen uns, potenzielle Schäden bereits im Vorfeld detektieren zu können. Mit Kameraüberwachung beobachten wir den Außenraum des Zuges und können so – Stichwort automatische Bilderkennung mit neuronalen Netzen – Abweichungen vom Normalzustand erkennen, etwa abgelöste Lüftungsgitter.
Viele weitere Beispiele lassen sich anführen. Im Zentrum steht ein Gedanke: Mit der flächendeckenden Ausrüstung von Sensorik wird das ganze System transparent: von der Weiche bis zur Lok. So entsteht die Basis für einen datengetriebenen, zustandsbasierten und vorausschauenden Bahnbetrieb.
Auch in der Automatisierungstechnik und Robotik gehen wir neue Wege, die etwa in der Automobilindustrie bereits beschritten werden: Roboter helfen den Mitarbeitern beim Bewegen und beim Einbau schwerer Teile, etwa beim Ein- und Ausbau von Türen und Fenstern oder der extrem unhandlichen Drehgestelle. Das alles entlastet die Mitarbeiter von körperlich schwerer Arbeit. Und wie in der Automobilindustrie führen wir unsere erste automatisierte Lackierstraße ein: Die Wagenkästen der ICE-Züge lassen wir in Cottbus künftig von Robotern lackieren.
Zudem werden wir nicht nur die Züge intelligenter machen, sondern auch die Werkstatt selbst: Wir werden Arbeitsabläufe vereinfachen, weil wir zum ersten Mal einen einzelnen Wagen aus einem ICE-Zug herausnehmen können – und das ohne Rangierarbeit. Wir schieben ihn quasi mit dem Gleis, auf dem er steht, seitlich aus dem Zug heraus.
Umbau von Dieselloks zu Hybridfahrzeugen
Es gibt ein weiteres Alleinstellungsmerkmal: Das Werk in Cottbus wird das einzige in Deutschland sein, in dem Dieselloks zu klimafreundlichen Hybridloks umgerüstet werden. Wir statten diese Rangierloks mit einem zusätzlichen Batterieantrieb aus. Damit senken wir den Dieselverbrauch und den CO2-Ausstoß um 20 Prozent. Dieses Verfahren eignet sich gerade jetzt für eine zügige Reduktion von Schadstoffen – für Lokomotiven, deren Lebenszeit längst noch nicht am Ende ist.
Digitalisierung und neue Technologien sind der Hebel, um den Schienenverkehr in seiner gesamten Dimension auf ein völlig neues Level zu heben. Das Werk in Cottbus wird zeigen, wie das geht. Und es wird weit strahlen, es kann – wieder einmal – ein Leuchtturm für deutsche Ingenieurskunst sein. Für die Bahn, für Deutschland, für Europa ist der Bau dieses Werks deshalb ein großer Schritt in die Zukunft.
Lesen Sie auch:
Artikel als PDF laden